HISTORY
The history of BMC runs deep in Wisconsin. In the years of the early 1900’s the Chier family was involved with mining bank sand in the Berlin, WI area. The bank sand was used by the foundry industry to make molds and cores used to produce iron and steel castings. Clifford A. Chier (C.A. Chier) saw the need for a higher quality sand for the foundry industry to reduce costs and produce higher quality metal castings. In 1946 C.A. Chier left a partnership he was in with a half-brother and purchased a high-quality silica deposit west of the village of Fairwater, WI. In the later 1950’s Clifford’s son Russell (Russ) joined his father in the family business. Together Cliff and Russ grew the high quality silica business throughout the State of WI. In the mid 1960’s Cliff’s son-in-law (George Hess) joined them in the business. In the early 1970’s C.A. Chier Sand Company saw the need to improve the quality of the silica they were selling to the foundry industry. At that time the foundry industry was going through innovative changes requiring a higher quality silica for use in chemical binder systems being developed. With this challenge, the C. A. Chier Sand Company developed the first hydraulic mining and wash plants in the State of Wisconsin. C.A. Chier Sand Company was the only silica operation in Wisconsin offering washed and dried high quality silica sand. Construction of a rail facility was completed allowing the Fairwater Plant to be served by the WSOR, a short-line rail system. This opened many new opportunities to serve the foundry industry outside the Wisconsin area.
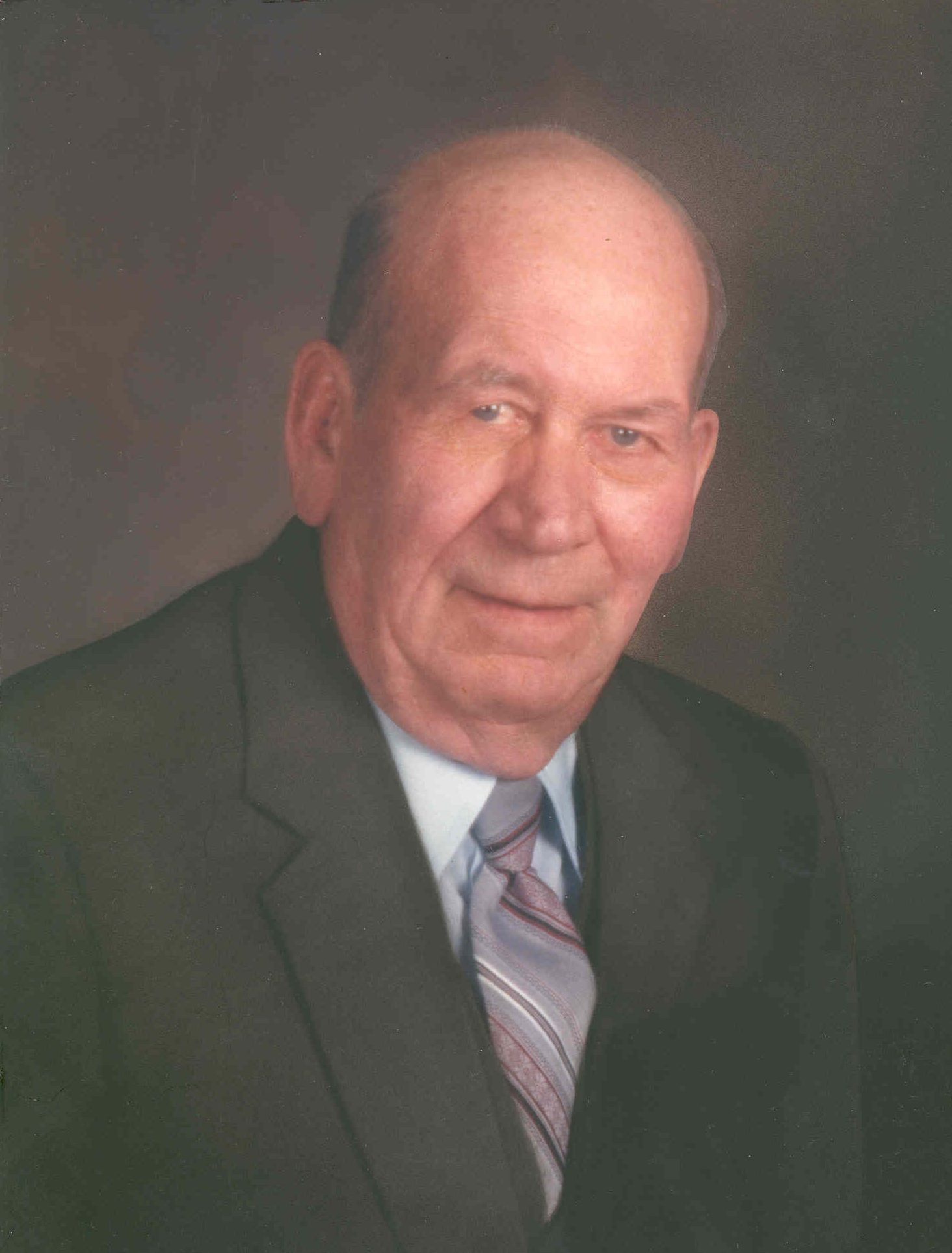
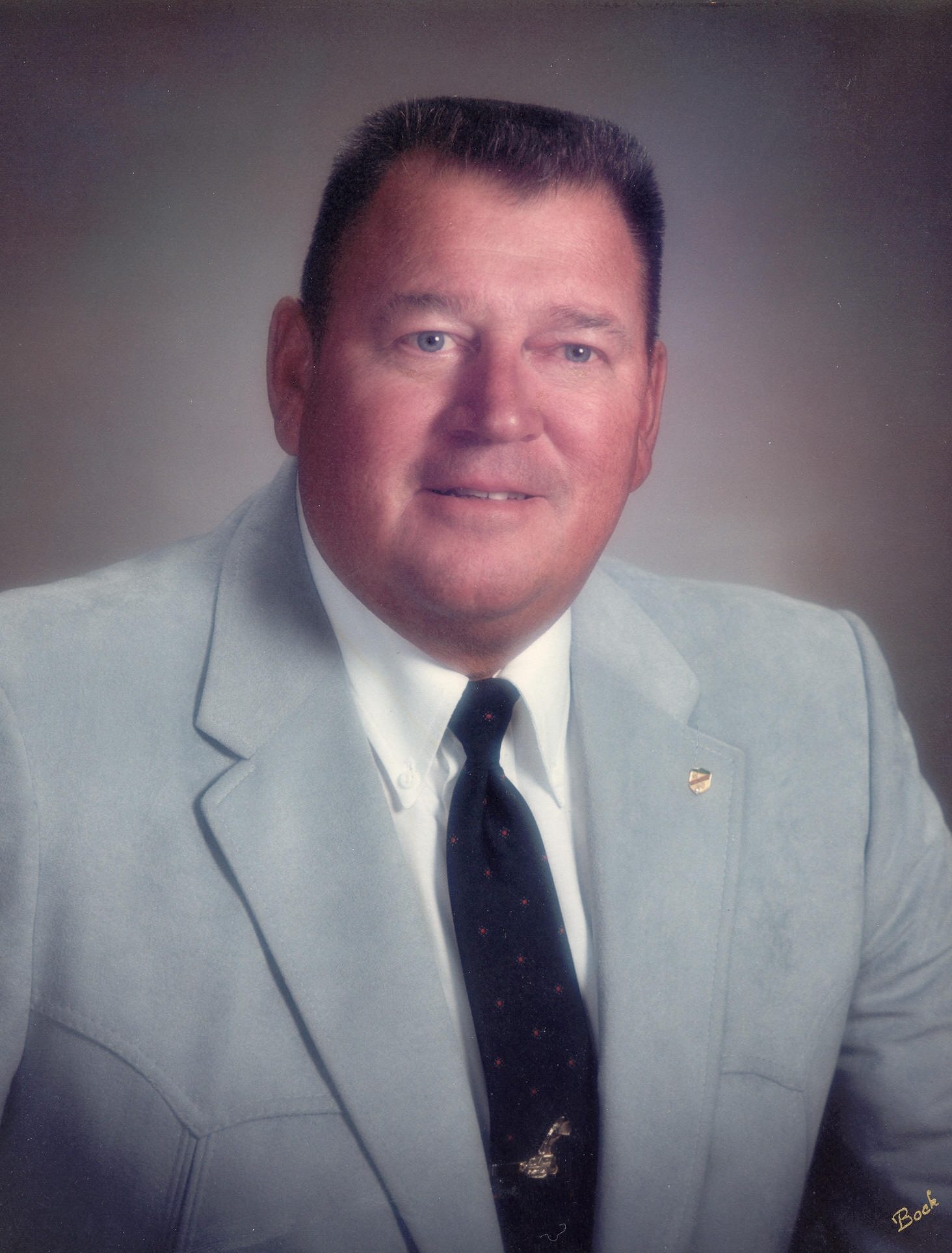
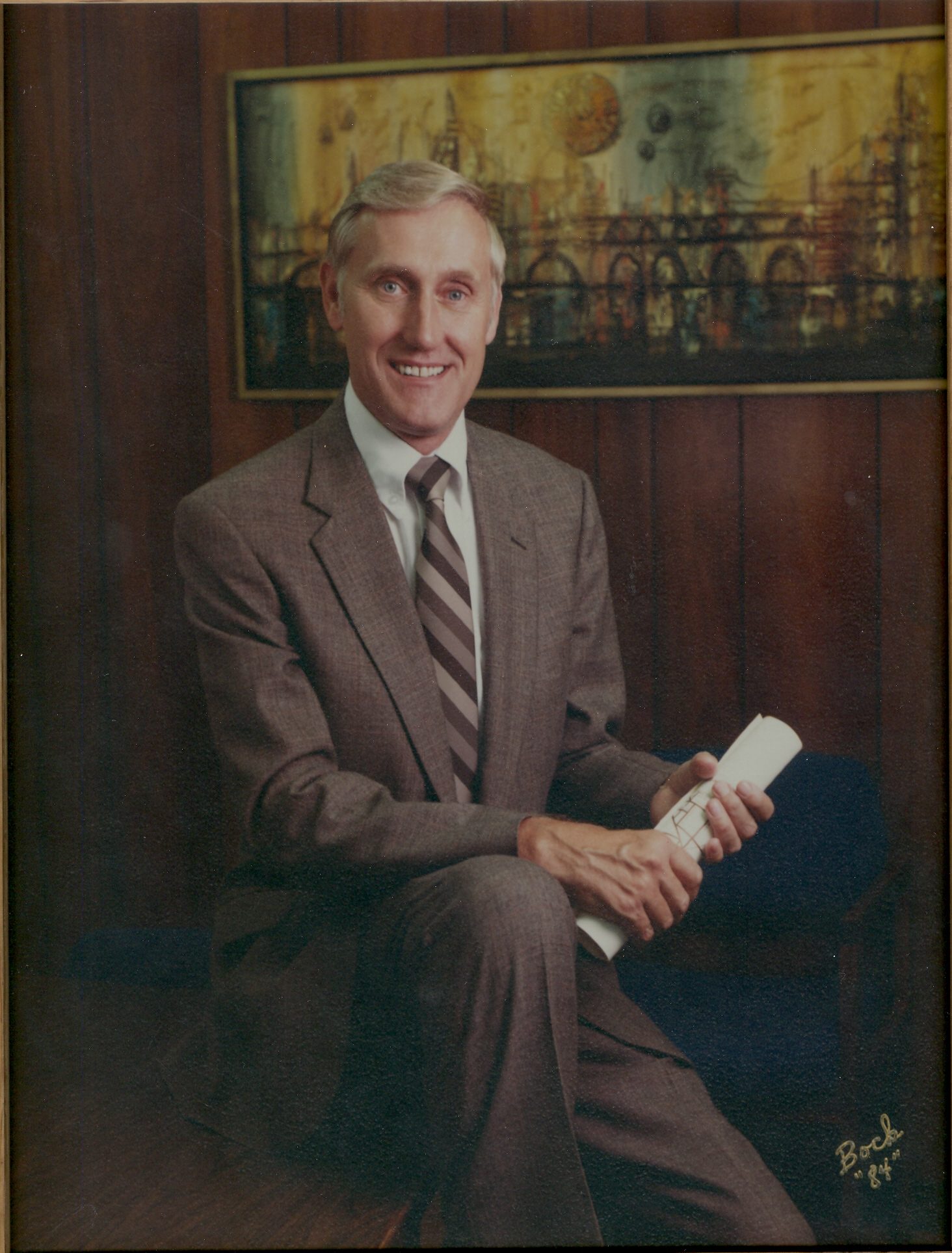
In 1979 Cliff made the decision to retire and turn over the family business to Russ and George, transferring ownership into the 2nd generation and into the Chier and Hess families. A decision was made to enter the gas and oil business with hydraulic fracturing sand. The company was incorporated, and the name was changed to Badger Mining Corporation. A plant was built near the village of Taylor, WI with the sole purpose to serve the frac sand markets in Texas. The Taylor Plant is located on the Canadian National (CN) rail line, a class-1 railroad serving Canada and many parts of the US. To serve the frac industry better BMC saw the need to build a number of transloads around the US and Canada.
In 1985, Badger Mining researched and implemented a new management philosophy using team concepts and principles. It was a new concept in management at the time and it has evolved through the years, but it is a philosophy that the company believes in and continues to use.
In the late 90’s it was decided that Badger Mining’s systems should be certified to an international quality standard. We chose QS900 as many of our customers supplied automakers and this standard was a requirement. Fairwater, Taylor and the Resource Center were certified to QS 9000 for many years. When the automotive industry developed a standard strictly for those supplying parts that go on the vehicles, Badger Mining became certified to ISO 9001. It is used as a total business system, not just a quality standard and remains certified today.
In 2005 BMC expanded its presence in the frac sand world by partnering to develop a resin coated sand company. The first plant was built near the BMC plant at Taylor, Wisconsin on the CN rail line. Capacity was quickly doubled at the Taylor resin coating plant and demand was high for product. Atlas then constructed a second resin coating plant near Merrillan, Wisconsin on the Union Pacific (UP) rail line. The UP allowed Atlas to better serve destination in southern US. Shortly after a third resin coating plant was constructed near plant number two. In 2015 Atlas Resin Proppants was merged into BMC bring resin coated along with raw sand to the marketplace.
In 2017 BMC saw the need to better serve customers in the Permian Basin of southwest Texas with the construction of a plant near Kermit, Texas. The Kermit plant is located in the northwest portion of the Permian Basin allowing BMC a freight advantage to serve many customers in that region.
BMC has Resource Centers (offices) located in Berlin WI, three sand processing facilities located in Fairwater, Taylor, WI and Kermit, Texas. BMC operates and owns several transload facilities throughout the US and Canada.
Today the ownership of BMC remains in the 3rd and 4th generations of Chier and Hess families.
THE MEANING OF BADGER MINING'S CREST
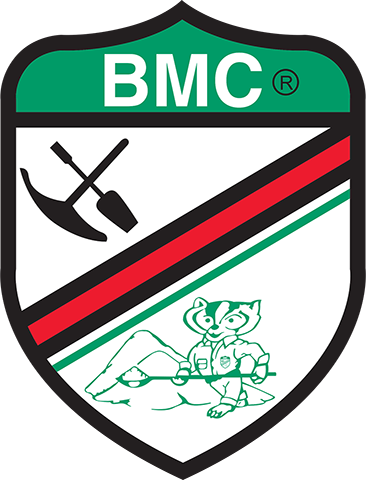
BMC: This stands for “Badger Mining Corporation.”
PICK AND SHOVEL: This is the universal symbol for the mining industry. The pick and shovel also remind us to stay within a business we understand.
BADGER: The Badger is BMC’s logo – an aggressive and courageous little animal who is not afraid of competitors or adversaries, even though they may be much larger.
BMC can certainly identify with the iconic Badger represented in the logo. Many of our competitors dwarf us in size, but BMC continues to prosper based on our core Values. It is also important to note that the original Wisconsin miners were called “Badgers” because of the holes they burrowed into the landscape near Mineral Point and Platteville from the late 1700s through 1978 when the last mine closed. That’s how Wisconsin got the name, “The Badger State.”
WHITE SPACE: This indicates high ethical standards, uncompromising commitment to safety, and high quality goals established by the Corporation.
GREEN SPACE: This identifies environmental responsibility: a lush, green, wholesome environment prior to and after mining.
RED BAND: This signifies the blood, sweat, and tears that have and will continue to go into corporate development.
SOLID BLACK BORDER: This represents the solid beginning and foundation given to us by our ancestors.